23 min read
The Impact of Completing Lean Training and How it Feeds into Team Standley’s 2024 Theme
By:
Kali Mogg
on
July 30, 2024
Updated: August 8, 2024
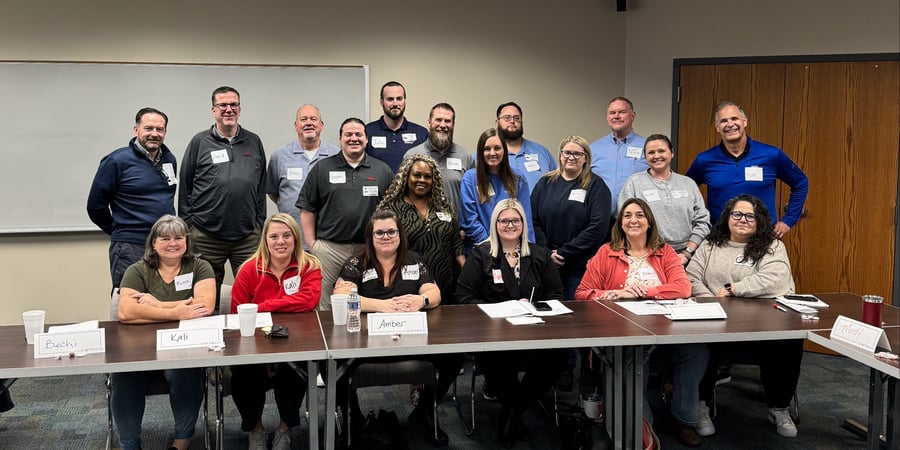
Imagine transforming your company into a powerhouse of efficiency and innovation, where every employee is empowered to drive meaningful change and operational waste becomes a thing of the past. Welcome to the world of Lean practices, where small, continuous improvements lead to monumental successes and an exceptional client experience.
Self-evaluation and setting goals for improvement and growth are crucial. Understanding where you are as a company and defining what success is and how to get there is something Standley’s executive team takes time to do each year during their yearly offsite planning session. It’s a time to look back and see where we have won and where we have room for improvement to make things better not only for our clients but for our team. In doing so the team defines a theme for the year and in 2024 we settled on “One Trip” as our theme.
The goal of “One Trip” is to do the job or process right, to the best of our ability and most efficiently on the first trip or time. When we accomplish the task or process on the first trip, touch or time we increase profitability and more importantly create an E4 experience (an exceptional experience, everyone, every time).
So how do we achieve “One Trip”? Cue the Lean process.
Understanding Lean Training
What is lean training?
Lean Process is an approach and method that works to eliminate wasteful use of resources plus defects in production processes to improve employee and company performance. It draws on the Lean concept of the 1940s which was established by Toyota in Japan to reduce waste and the Six Sigma strategy of the 1980s where Motorola set out to reduce defects. Lean is a system designated to reduce waste through continuous improvement that's driven by what the customer wants. It produces standardization which gives way to continuous improvement.
The Lean process is made up of five “S”:
- Sort
- Set in Order
- Shine
- Standardize
- Sustain
Sort and eliminate waste and set in order what is left. Then, shine by cleaning and inspecting. When you standardize you set the rules. The first three “S” are set by the employee or person doing the work. Last, sustain by maintaining the standard with routine walkthroughs.
These five "S” or principles are the steps which practitioners take to create a more efficient process and a workplace culture of continuous improvement.
So why is it crucial to deploy techniques and methodology like Lean? Every company or business in every industry across the globe has processes that need to be improved. Lean exercises the best problem-solving methods to assist organizations in achieving their goals and ensuring that customers receive an exceptional experience.
Benefits of Lean Training
There is no ceiling to the benefits of implementing lean process and training for continuous improvement. When you are continuously looking for ways to improve your process it results in a better customer experience. That’s the goal for Team Standley, to produce an exceptional experience for everyone every time.
Not only does Lean produce benefits for the client but also your employees. When you engage your employees in the solution, it improves morale, culture and develops your team members. Breaking down a process encourages individuals to strengthen their critical thinking and enhance problem solving skills.
Overall Lean produces:
- Streamlined processes which improve customer experience and brand loyalty
- Process standardization produces agility or nimbleness, giving you the ability to pivot to everyday challenges (enhanced problem-solving and critical thinking skills)
- Increases capacity and profitability
- Increases effectiveness
- Engaging employees in the effort improves culture and employee development
- Develops effective people and teams by building confidence and capability of teams. Makes everyone feel like they play an integral part in pushing the needle forward.
-
- “All In”
-
- “What I do matters”
By leveraging and implementing Lean methodologies the organization, employee and customer all win.
Now that we better understand what Lean is and why it is crucial in creating an exceptional experience and culture. Let’s walk through how Team Standley bought in and implemented these methodologies to improve our process and service.
A Day in the Life of a Lean Trainee – Team Standley Edition
Trainees were divided into three teams that were composed of team members from different departments across Standley Systems. 69 members of Team Standley completed Lean training representing all 11 departments across our organization including our executive team. Each group met on different days but completed the same exercises and material in a full day offsite.
Teams started the day with a new hire orientation where they were debriefed on a fictious organization that they would be working for throughout the duration of the training.
The orientation consisted of:
- Assigning each person to a job function/role
- Hearing the business objectives
- Reviewing company policies
- Understanding the layout of the facility
- Learning product information which included
- Cost
- Assembly
- Distribution
Once orientation was complete, trainees left the training room and entered a replica assembly line for the first of three rounds of simulation. Each team member had a specific job and role with instructions and a timeframe to complete the simulation of assembling and distributing customer orders.
After the first round was complete, the team went back to the training room to discuss the simulation and get feedback about what worked and didn’t. The team took that feedback and developed new processes and workflows then went back into the simulator for round two.
Pictured: Team Standley in one of three rounds of simulation
Once round two was complete they repeated the process of continuous improvement through each member’s feedback and observations. By the end of round three the teams drastically improved their process through standardization and the five “S” of Lean, which in turn improved their production and distribution time along with the quality of their product.
Team Standley Leans into Process Improvement
After each team member completed the training process they were encouraged to go back to their role and look at each of their processes through the lens of the five “S” of Lean.
One way that Lean is being implemented is in achieving Standley’s “One Trip” initiative by streamlining and standardizing our paperwork and order process. After the training, Team Standley began meeting with all departments and key players in our paperwork process.
This team met various times throughout the first quarter to unpack the paperwork process, make improvements, test those improvements and then reconvene for feedback and to implement more improvements. This team meets at the end of each day to look at how the day went with order processing and what might need attention. In just a few months' time the team has improved their first pass yield of processing orders by 11%.
Another way we are practicing what we learned is by being active members of Continuous Improvement Oklahoma (CIOK).
What is Continuous Improvement Oklahoma? It is a consortium of Lean practitioners that come together to grow their Lean knowledge and implementation efforts. As an CIOK member you:
- Share Lean best practices with other Lean practitioners.
- See how various facilities in different industries use Lean.
- Receive constructive suggestions on how you can improve your operation.
- Grow your Lean Network.
CIOK is led by members of industry and sponsored and supported by the Oklahoma Manufacturing Alliance and Francis Tuttle Technology Center. CIOK has been an asset to us as it provides a place for our team to chat with other Lean evangelists and gives us the opportunity to see Lean process in play in a variety of industries and settings.
Practicing Lean is only half of the equation though. To continue to produce and implement change, we must track how we are doing and be nimble enough to pivot when necessary.
Lean isn’t One and Done – How We Track Our Progress
Continuous improvement isn’t one and done. It is a daily pursuit to get better even if it's just by 1%. Tracking is an important piece of improvement and to track how we are doing our team has created various dashboards.
How do these dashboards help?
- Bring visibility to the processes
- Create companywide accountability
- Give everyone involved a way to see data in a tangible, understandable format
- Help in setting goals and mile markers
What have our dashboards told us so far? That we were able to improve first pass yield for order processing by 11% in just three months, which means a smoother transition from the time an order is placed to install and implementation for our clients.
We Promise to Keep Pushing Forward
Embracing Lean processes is not just about cutting costs or eliminating waste—it's about fostering a culture of continuous improvement and empowerment. By implementing Lean practices, you can unlock the full potential of the workforce, drive innovation, and achieve sustainable success. The journey may be challenging, but the rewards are transformative, leading to a more efficient, productive, and engaged organization.
Team Standley, is grateful for the opportunity to learn and implement Lean processes. This journey has not only equipped us with invaluable skills but has also strengthened our ability to work collaboratively towards a common goal of “One Trip”. By embracing Lean principles, we are committed to creating an exceptional experience for everyone, every time. Our dedication to continuous improvement and teamwork ensures that we deliver the highest quality service and innovation, providing our clients with relevant solutions and generous service while empowering our employees.
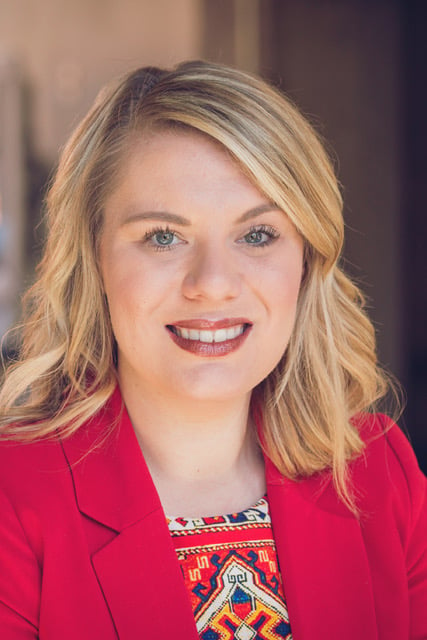